You’ve got questions.
We’ve got answers.
Can Brightmark accept plastic waste for recycling from Thomaston’s local citizens? What would be the requirements?
Brightmark can accept mixed-stream plastics from sources like curbside recycling from local communities and plans to work with local waste haulers from the Thomaston area to receive and recycle plastics.
Brightmark intends to work with government officials from Thomaston to understand the community’s recycling needs in order to develop requirements that can cater to community members seeking to recycle plastic waste.
How much plastic waste will the Thomaston Circularity Center recycle?
Once complete, the Thomaston Circularity Center will have the capacity to convert 400,000 tons of plastic waste (equivalent to the weight of 100 of the retractable roofs on Mercedes-Benz Stadium) into new, circular products yearly—diverting plastic waste from landfills, incinerators, and the environment.
When is the project expected to be completed?
The projected timeline for the project is as follows:
- Approximately 2 years for permitting the facility, followed by a groundbreaking
- Approximately 2.5 to 3 years to fully construct the Thomaston Circularity Center
How will the size of this center compare to Thomaston’s local Walmart?
The building on-site will be larger than Thomaston’s local Walmart. The 2.5 million-square-foot circularity center will encompass the entire footprint of our site. This includes all buildings, exterior equipment, parking, rail, and roadways. An enclosed building will be nearly 300,000 square feet, with the remaining square footage dedicated to exterior equipment.
What was the strategy behind waiting for the public announcement of the Thomaston Circularity Center?
Brightmark and the Thomaston Industrial Development Authority (IDA) spent ample time ensuring synergy between Brightmark and the Thomaston community. This included understanding the community’s needs, values, and the viability of bringing circular innovations to Thomaston. The IDA took time to understand Brightmark’s technology, including a visit to the Ashley Circularity Center to understand how the center will benefit the Thomaston community.
How is Brightmark providing more transparency on these facilities for the Thomaston community?
Brightmark hosted the Thomaston Industrial Development Authority (IDA) board multiple times at its circularity center in Ashley, Indiana. This visit further educated community leaders on Brightmark’s technology, operations, and safety protocols—and gave them first-hand experience of Brightmark’s recycling process.
“After a comprehensive two-hour tour of the Brightmark Facility in Ashley, it is clear to me that their proposed facility would be an excellent addition to our Business and Technology Park. Their innovative product, rigorous operational standards, and intense commitment to safety exceed that of most companies I have seen in my career managing counties.” Jason Tinsley, County Manager, Upson County Government
What positive impacts will Brightmark have on the Thomaston community?
Brightmark values the communities where it works and operates and wants to be a strong, long-term community partner.
Economic Investment: Brightmark plans to invest $950MM to develop a circularity center in Thomaston. Brightmark will also invest $20MM in infrastructure project upgrades, like utility updates and roadway improvements.
Career Opportunities: The circularity center will create hundreds of construction jobs and nearly 200 manufacturing jobs.
Community Partnerships: Collaborating and partnering with the Thomaston community is essential to Brightmark. We work with and support diverse entities that focus on community initiatives dedicated to environmental conservation, education, and social responsibility. From the Georgia Recycling Coalition to Drawdown Georgia, Brightmark focuses on building meaningful partnerships that positively impact the community.
What is Brightmark’s process for engaging with the community?
Georgia’s growing demand for the environmental technology sector made the state an attractive place for the company to invest significantly. Brightmark chose Upson County, specifically the Thomaston community, to build its flagship circularity center because of its homegrown talent and the desire to grow with a strong community partner. Brightmark has been actively working with Thomaston government officials and advisors to engage with the community and future employees as Brightmark integrates itself as a long-term community partner.
What types of organizations are Brightmark considering collaborating with in Thomaston?
Brightmark’s community efforts span an array of initiatives from education to conservation. We’re exploring opportunities with various organizations that have a strong community presence throughout Thomaston and the greater Georgian region. This includes Southern Crescent Technical College, with whom we aim to develop programs focused on education and workforce development. Organizations like Southern Crescent have specific goals, missions, and values that align with Brightmark’s goal of creating a world without waste.
How will Brightmark handle the disposal of leftover materials?
Our Thomaston Circularity Center will have limited leftover materials. Our process is highly efficient, with most of the material (plastic waste) being converted into new, circular products. Occasionally, materials not fit for our process end up in our center. When this happens, we will look to work with other recyclers who can process them. In addition to that, approximately 10% of the remaining will be a non-hazardous, solid inert residue (SIR) that can be safely landfilled. Brightmark is exploring opportunities outside of landfill disposal for the SIR to create the most appropriate solution for the environment and community.
Do Brightmark’s operations produce fuels?
Brightmark’s operations do not produce fuels. The circularity center in Ashley, Indiana, was initially designed to produce ultra-low sulfur diesel (ULSD), naphtha, and wax. All production runs at the center have produced International Sustainability and Carbon Certification (ISCC) PLUS certified circular pyrolysis oil, used to make new, circular products and not used as fuel for energy.
What is the end product of the plastic when it is recycled?
Brightmark is producing ISCC PLUS certified circular pyrolysis oil which our customers can use to produce circular plastic products.
Why is Plastics Renewal® important?
The United States is facing a major plastics recycling shortfall. Communities are struggling with an accumulation of plastics that are filling up incinerators and landfills. More than 95% of plastic produced in the U.S. each year is not recycled.
Millions of tons of plastics end up in landfills, are burned, or end up in the environment every year. A staggering 8 million tons of plastic end up in the ocean annually—and that number is rising. If plastic waste streams aren’t managed, there will be more plastic in the ocean than fish (by weight) by 2050.
A key reason for plastic pollution is that the raw materials in plastic have been completely devalued, and most plastic types can’t be recycled with traditional mechanical methods. But Brightmark’s Plastics Renewal® technology solves challenges historically associated with recycling plastic, and it recaptures the inherent value in the natural resources used to manufacture plastic. Brightmark’s proprietary advanced plastics recycling technology can produce the building blocks necessary to manufacture plastic again, creating a circular economy technology for plastics.
What is Plastics Renewal®?
Brightmark’s Plastics Renewal® technology is based on pyrolysis, which is defined as the process of subjecting substances to very high temperatures without oxygen to facilitate their chemical decomposition.
There are three main steps in our Plastics Renewal® process:
- Plastic waste is purchased and prepped for conversion by removing metals and other non-plastic materials; then, we dry and shred the plastic and compress it into pellets.
- The plastic pellets are heated and vaporized in an oxygen-starved environment.
- The released vapor is captured and cooled into a hydrocarbon liquid, then processed into circular pyrolysis oil.
What makes Plastics Renewal® different?
There are several key areas of differentiation of Brightmark’s technology.
The most important difference is efficiency. A common criticism of advanced recycling technologies is that they require more energy than they produce, but that is not the case with our technology. For every unit of energy input for our process, we produce 11 units of energy.
Another key differentiator is that we can continuously operate our production line with mixed-stream plastics 1 through 7—which many other recycling processes can’t accept. We can take any plastic, from bottles to car seats, which includes the types that are traditionally difficult or impossible to recycle.
Finally—and this is what it all comes down to—we have a circular solution that’s creating a world without waste. It solves a major societal problem and creates value from a common but devalued material.
What kinds of plastic can you recycle?
Brightmark takes plastics from all streams—plastics 1 through 7—and combines them into a single output that can be turned into new products.
The potential impact of this technology is incredible: the old yogurt container that would have previously ended up in a landfill because it couldn’t be recycled, only to later turn into microplastics, can now be used for something new. This innovation will positively impact the lives of people for generations to come.
Where do you get your plastic from?
Brightmark takes plastic from all streams. The Thomaston facility will source plastics from the southeast region of the United States, which our research shows will provide ample quantities of plastic waste to convert.
Does any plastic waste come directly from other countries?
Brightmark does not receive plastic waste from other countries. The Thomaston Circularity Center will prioritize sourcing plastic waste from the Southeast region of the United States.
How is the plastic waste prepped before processing?
Brightmark has a preprocessing system for plastic waste, which includes separating metal and nonmetal materials and other unusable waste from the plastic. Plastic waste is then shredded, pelletized, and fed into Brightmark’s patented pyrolysis conversion units.
Are the plastic components from electronic waste separated before arriving at Brightmark’s circularity center in Ashley, Indiana? If not, what happens to the nonplastic parts?
Brightmark does not accept electronic waste. We work strategically with our suppliers and partners to separate electronic waste into plastic and non-plastic streams before plastic streams are sent to the circularity center.
We work with materials recovery facilities that can recover non-plastic parts from electronic waste. For example, our local partner in Indiana, RecycleForce, separates plastic from electronic items to recover precious metals and other components. This system helps reduce waste by recovering and recycling usable materials.
Does this technology pollute the air and water?
All manufacturing processes create some air emissions. However, the Thomaston Circularity Center is committed to having a low environmental impact. Our center’s emissions are similar to those of a medium-sized hospital. Specifically, our circularity center in Ashley, Indiana, is considered a synthetic minor source emitter under the Clean Air Act, and we anticipate that our Thomaston Circularity Center will fall under the same category. The primary source of these emissions comes from the heat used to dry the plastic and operate the equipment. A recent third-party analysis showed that our liquid output is 39% to 139%1 less carbon-intensive than traditional methods of petroleum production.
Out of what we produce, 93% of the feedstock materials in Brightmark’s facility come out as new products—with the other 7% ending up as waste that can be safely landfilled.
Because we are committed to protecting the local environment, especially the Flint River, we are investing millions to ensure that all wastewater is kept separate from any municipal water. We are investing over $1MM in a Zero Liquid Discharge (ZLD) technology process wastewater system in Thomaston where all process wastewater will be processed and managed on-site and will not impact or be released into the local community or municipal water supply, including drinking water, groundwater, or local waterways.
1Scale is based on respective EU and U.S. categorization of waste solutions.What products do you produce?
Our Thomaston facility will convert discarded plastic materials into new, circular products. Additionally, Brightmark’s proprietary advanced Plastics Renewal® technology can produce the materials needed to manufacture plastic again, creating a circular economy technology for plastics. We strive to make Thomaston a center of Plastics Renewal® innovation.
Isn’t this just incineration?
Incineration uses oxygen in the process of burning materials like plastic to create heat. Incineration is a high-carbon emission process that is often used in the waste-to-energy industry. We don’t do that.
Our process has a significantly reduced carbon intensity compared to other methods for extracting the petroleum products used to make plastic. Our Plastics Renewal® process does not involve incineration or combustion, and we are classified as a synthetic minor source emitter under the Clean Air Act.
Our technology uses the process of pyrolysis to break the chemical bonds in plastic in the absence of oxygen so that the raw materials can be broken down into their original chemical chains, can be recaptured, and then transformed into new products.
Does Plastics Renewal® contribute to the climate crisis?
All manufacturing processes create some greenhouse gas emissions, but independent analysis confirms that Brightmark’s Plastics Renewal® process produces major savings compared to other processes that produce similar products.
The main finding is that our process produces 39% to 139%1 less greenhouse gas emissions than equivalent products made from virgin materials.
The life cycle analysis also revealed that our Plastics Renewal® technology provides:
- 82% energy use savings2
- 46% water use savings2
Simply put, products created by Plastics Renewal require only 17% of the amount of fossil fuels needed to make plastics from virgin petroleum.
Plastics Renewal® is a world-changing technology. It keeps natural resources in use via the circular economy while reducing the need for fossil fuel extraction. These types of actions help to limit climate change.
1Scale is based on respective EU and U.S. categorization of waste solutions.2Life cycle analysis conducted by Environmental Clarity Inc. and peer-reviewed by a Georgia Institute of Technology faculty.
Does Brightmark support the reduction and reuse of plastic?
Brightmark fully supports efforts to reduce plastic consumption. Brightmark’s technology focuses on recycling difficult-to-recycle plastics—used in essential industries like healthcare, manufacturing, and packaging. These plastics are vital to the economy and the products people need and use. That’s why responsible and viable ways are required to recycle these materials properly—allowing essential industries to operate while providing a circular solution to divert plastic waste from landfills, incinerators, and the environment.
Does this technology have a place in the circular economy?
Yes, it does.
Brightmark is a circular innovation company that creates solutions to eliminate waste and give existing plastic materials a new life. We’re disrupting waste streams wherever we see that we can make an impact with traditionally difficult-to-recycle items like children’s car seats and boat shrink wrap.
Our Plastics Renewal® technology can take all types of plastic, including mixed plastics 1 through 7, and convert them into new products. We will make Thomaston home to one of our circularity centers to help us continue our journey of Reimagining Waste.
Revised: November 18th, 2024
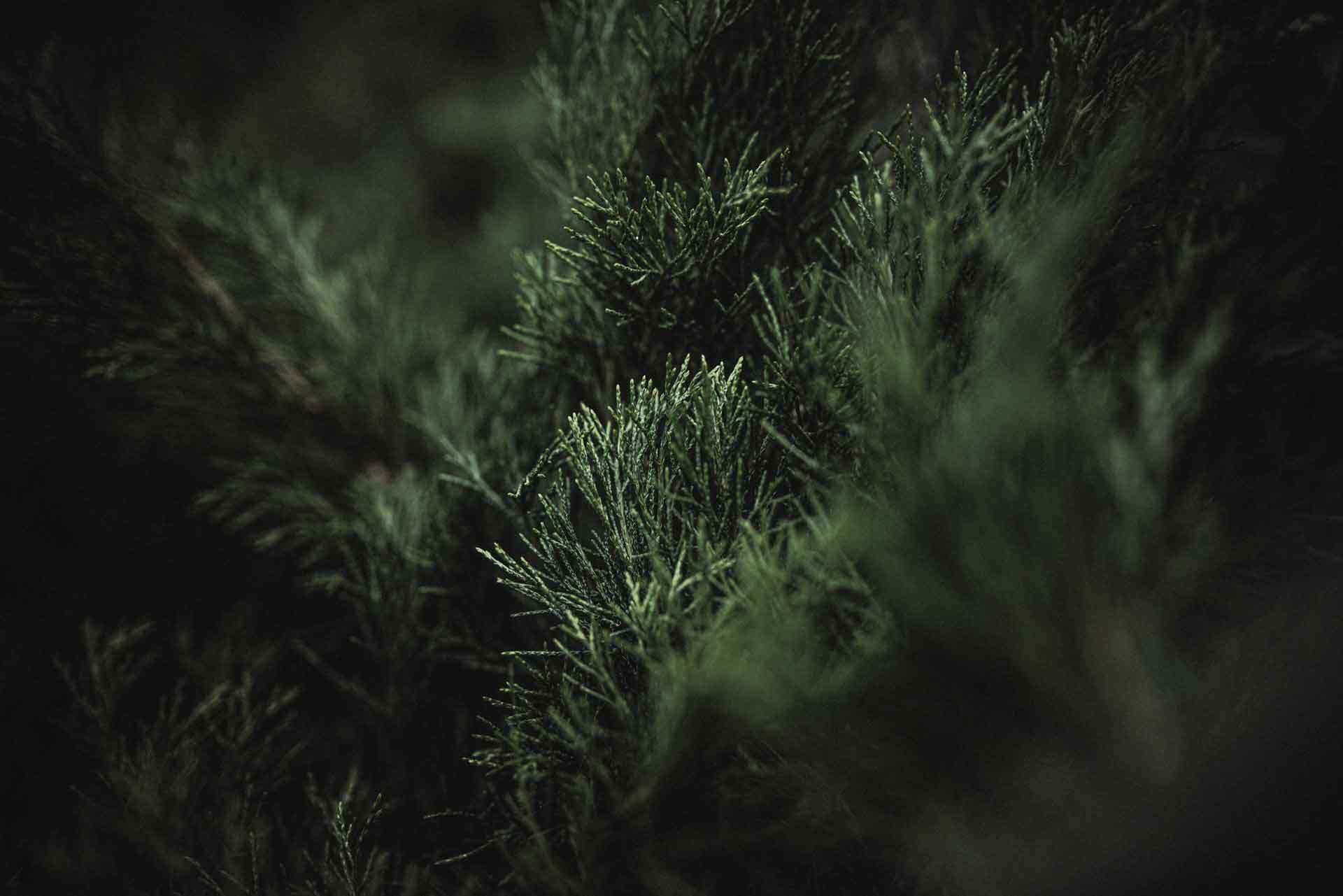
“I’ve had the privilege of building relationships with Brightmark team members who have actively engaged with our community by volunteering at local events, supporting local businesses, listening to residents, and understanding our needs. This billion-dollar investment in our community will not only double our tax digest but also shine a spotlight on our area, attracting even more job opportunities and economic growth. I am confident that with the support of the State of Georgia, the City, and the County, the future is bright for this new development.”
JENNIFER ROGERS
Thomaston-Upson Industrial Development Authority Member